Designed and Hand-blown individually by Oliver Höglund & Ryan Roberts.
Made in Currumbin, Australia
Each piece made is different to the next, giving you a truly original piece of functional art.
Statement wall & pendant lighting that enhances your space with a unique ambience.
Statement wall & pendant lighting that enhances your space with a unique ambience.
Featured in
ABOUT US
Oliver Höglund and Ryan Roberts are the creative minds behind SØKTAS, and the company’s inception began in Oslo, Norway where they first met in 2015. SØKTAS is a reflection of both their stories and visions. Third Generation Glass Artist, Oliver's craft has been passed down to him from his Father, Ola Höglund & grandfather, Erik Höglund. When purchasing our lights you get a unique story and a timeless piece of art.
The skills and techniques learned by Oliver since 2001 have allowed him to develop his craft and create his own signature style. The process of hand-blowing glass is rigorous and intense, as the molten hot glass is shaped and blown by hand at around 1000° C by Oliver himself.
The skills and techniques learned by Oliver since 2001 have allowed him to develop his craft and create his own signature style. The process of hand-blowing glass is rigorous and intense, as the molten hot glass is shaped and blown by hand at around 1000° C by Oliver himself.
Made in Currumbin, Gold Coast.
COLLECTION
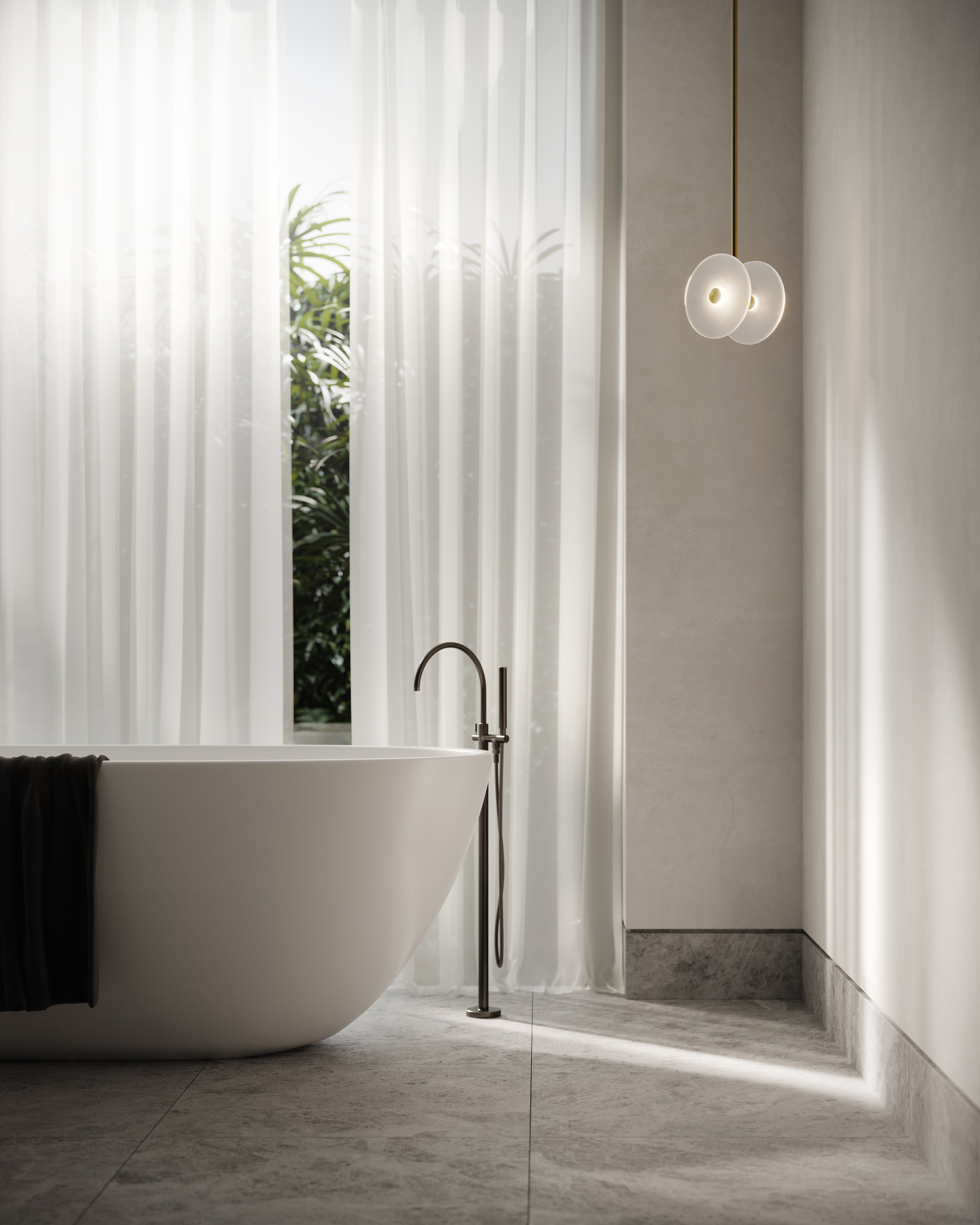
REVIT & SKETCH UP FILES
Please email ryan@soktas.co for our latest REVIT & SKETCH UP Files to add to your renders and plans.
FOLLOW @SOKTAS ON INSTAGRAM
Click an image to shop products